What is propellant gas?
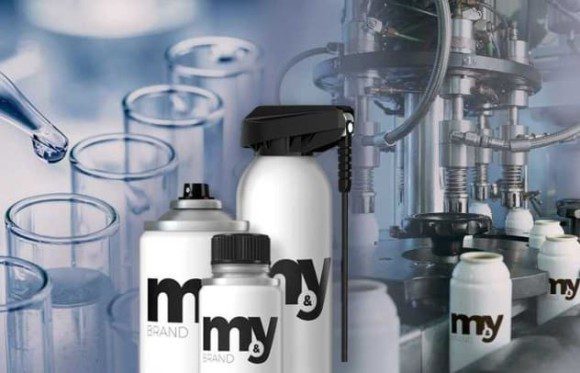
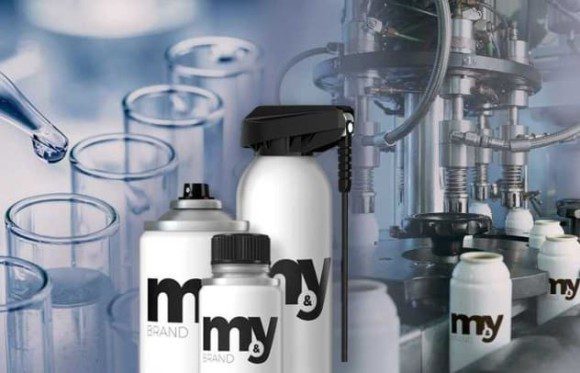
Propellants, also known as propellants, are placed in the category of intermediate hydrocarbon branch, which, after purification, do not harm the ozone layer when released. For this reason, they have a wide range of applications worldwide. Propellants are known as the “propelling force” in industries and do not leave any side effects after use.
Propellants serve as a carrier gas and provide controlled pressure and spraying in cosmetic and personal care industries, perfumery, food and pharmaceutical industries, various industrial sprays, adhesive industries, paint and varnish industries, cleaning and cleansing industries, as well as industries producing pesticides. Nowadays, sprays have extensive applications in various industries as well as in daily life. One of the most important reasons for this is the ability to use sprays in cases where the main substance needs to be used in a specific amount and locally in a large volume.
The contents of sprays consist of two main elements regardless of their application:
- Main Product: The formula of the substance that the manufacturer intends to sell.
- Propellant Gas: A gas that is used as a source of pressure inside the spray can.
The uniform combination of these two aerosol dispensers is called a spray.
As mentioned, aerosols are essentially very fine liquid and solid particles in gas form that are dispersed uniformly in the air and their environmental stability depends on the particle size and the effect of gravity on these particles.
Aerosols are prepared by natural agents or devices and are classified into different groups based on particle size. They can be divided into two general categories: good aerosols and bad aerosols. However, aerosol technology is used in various fields such as military, agriculture, cosmetics and personal care, medical and pharmaceutical industries, production of medicinal sprays, and more.
Obtaining a homogeneous and uniform solution of the propellant and the main product is one of the most important parameters for achieving optimal formulation in aerosol formation.
General Specifications of Propellant Gases:
As mentioned, propellant gases are the primary substances used to provide pressure inside the aerosol cans.
Physically, propellant gases can be in two different states:
- Liquid Phase: In this state, the propellant fluid turns into a liquid due to pressure and is used. An important point in these conditions is to use gases that are usable in a specific pressure inside the can and at room temperature in equilibrium between gas and liquid. In these conditions, when using the spray, the pressure of the propellant gas collected at the top of the can decreases, and this pressure reduction in the gas-liquid equilibrium conditions results in the evaporation of some of the propellant gas, and the pressure drop will be compensated.
Due to the use of liquefied gases in this state, there will be a higher volume of propellant fluid in the spray, and therefore, the lifespan of the spray increases, and the discharge pressure remains almost constant throughout the lifespan of the spray. These advantages have led to the widespread use of the liquid state in the aerosol industry. Propellant gas is classified in this category of propellant gases.
- Gas Phase (Compressed Gas): In this state, the propellant fluid exists as a compressed gas inside the spray container. After using the spray in these conditions, the propellant gas pressure decreases slightly, and over time, the efficiency of the spray decreases, and the lifespan of the usage cycle decreases. The presence of these disadvantages and the use of special nozzles to adjust the pressure have limited the use of this compressed gas state.
Propellant gases must have specific properties that are essential in all physical states and industries:
- No chemical reaction with the can and nozzle equipment.
- No severe toxic properties.
- High purity.
- Odorless in most applications.
- Reasonable cost.
- Availability.
Classification of propellant gases based on formulation and related industries:
The gases used in aerosol industries as propellant gases have undergone significant changes from the time of the first aerosol production until today and have various classifications, some of which are now considered outdated.
The main type of these classifications is the classification based on the chemical formulation of propellant gases.
Based on this, the chemical classification of prominent propellant gases is as follows:
- Hydrocarbon Gases: Hydrocarbon propellant fluids are composed of two major categories of intermediate distillation products: propane and butane (butane in both isobutane and n-butane forms), which are used separately or in different percentages.
Hydrocarbons are derived from crude oil and have been used as propellants in aerosol industries for years. Hydrocarbon propellants have a reasonable cost and availability and are known as propellants in this industry by the name of aerosol propellants.
In addition to the mentioned properties, these gases do not react with the surrounding objects when in contact and do not harm the Earth’s atmosphere, unlike CFCs.
The disadvantages of hydrocarbon gases are their flammability and the fact that they do not dissolve in water. For this reason, they are not used in sprays whose main ingredients include water. However, the two-phase state of these gases significantly enhances the efficiency of sprays, thus increasing the variety of products in this industry and contributing to market development.
Industries that use hydrocarbon gases as propellants include dyeing, cosmetics and personal care, pharmaceuticals, edible sprays, some chemical industries (insecticides), and more.
- Dimethyl Ether (DME): Dimethyl ether is another propellant gas used in aerosol industries. It is also derived from petroleum hydrocarbons and is water-soluble. For this reason, it is used in industries where the main component of the spray is water. Also, due to the water solubility, its flammability is lower than hydrocarbon propellants.
The problem that dimethyl ether faces in the aerosol industry is its high production cost and complexity compared to hydrocarbon propellants.
Dimethyl ether is used in some personal care industries that are water-based and in special spray industries such as color dyes soluble in water. However, it is also possible to use it for all products produced with propellants.
- Carbon Dioxide, Nitrogen, and Dry Air: Carbon dioxide and nitrogen gases are used as propellants either in combination or separately in some industries.
The advantages of using these two gases include cost-effectiveness, availability, and their non-flammable nature. Some special sprays in the cosmetics and personal care industry, such as facial sprays, sprays used in the food industry, and fire extinguishing capsules, utilize these gases and their combinations.
The problem with these two gases is the difficulty of using them in liquid form due to the high pressure and low temperature required, which necessitates the use of thick capsules (fire extinguishing) or short usage cycles for sprays (skin treatment sprays). Additionally, the efficiency of sprays produced with these gases is low, and part of the contents does not spray out due to pressure decrease.
- Chlorofluorocarbon (CFC), Hydrofluorocarbon (HFC), Hydrofluoroalkane (HFA): The use of these gases dates back to the history of aerosol production. Chlorofluorocarbons were initially used as propellants in aerosols after Dr. Frank Sherwood Rowland and Mario Molina announced in 1974 that chlorofluorocarbons used as propellants in aerosols were causing ozone layer depletion. Doubts about using these gases in the industry began, and from 1995 onwards, with the Montreal Protocol and the damage caused to the ozone layer, their use became highly restricted and eventually prohibited. During this period, industries managed to replace the mentioned gases with alternative ones.